We use cookies on our website to give you the most relevant experience by remembering your preferences and repeat visits. By clicking “Accept”, you consent to the use of ALL the cookies.
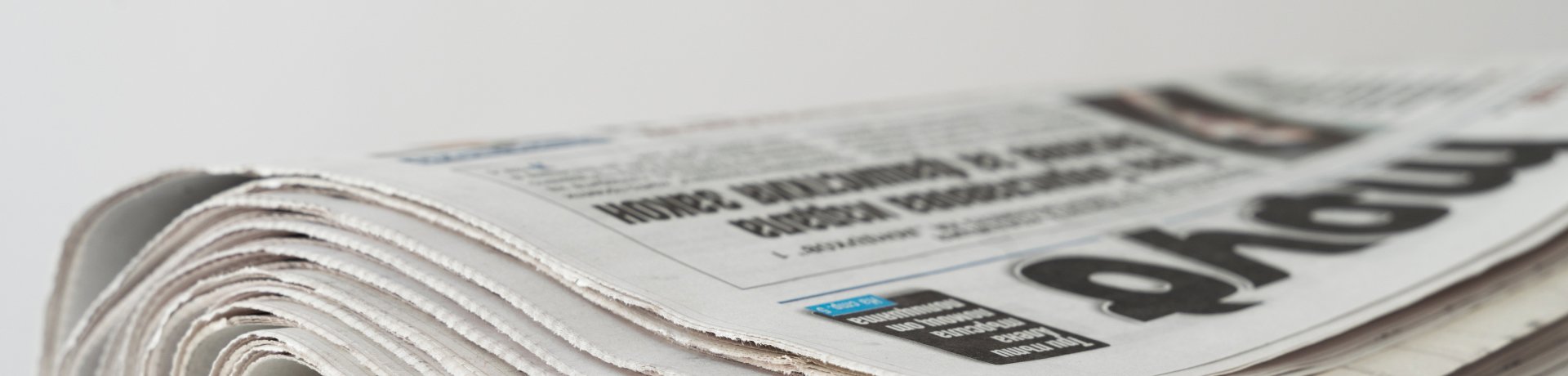
As a custom metal parts manufacturer established in 1996, Kailai Machinery has been deeply involved in the field of metal manufacturing for many years, and is proficient in metal stamping, stretching, welding and common surface treatment, especially focusing on stamping process. Today, we will focus on the R angle processing of small batches of goods-when customers do not want to invest in mold costs, how bending machines can become the preferred choice with flexibility, and also objectively analyze the difference in precision between mold processing and bending processing.
The core difference between mold processing and bending processing: the game between precision and flexibility
In the R angle processing of metal parts, mold processing and bending machine processing have their own focuses. The advantage of mold processing is that the precision is extremely high. Once the mold is debugged, the R angle size and curvature of each part produced can be highly consistent, and the error can be controlled within a very small range. It is an ideal choice for products with large batches and high precision requirements. However, the shortcomings of the mold are also obvious: a set of molds can usually only correspond to R angles of fixed specifications. If the angle needs to be adjusted, the mold must be redesigned and manufactured, which is not only costly but also prolongs the production cycle, which is undoubtedly a heavy burden for small-batch processing.
The core advantage of bending machine processing lies in flexibility. Especially for R angle processing of small-batch goods, it can quickly respond to different R angle requirements without investing in expensive molds. Although bending processing is slightly inferior to mold processing in terms of accuracy, and the error is generally slightly larger, for most small-batch products with non-extreme precision requirements, such accuracy is sufficient to meet the use needs. In many years of metal manufacturing practice, we have found that through reasonable operation, the R angle accuracy of bending machine processing can fully meet the general standards of small and medium-sized batch products in the industry.
Bending machine realizes multi-angle R angle processing: replacing the blade is the key
To make the bending machine fully flexible in small-batch R angle processing, replacing the bending blade is the core skill. Different specifications of R angle correspond to different arcs and shapes of cutter heads. By quickly changing the cutter heads, the bending machine can switch processing modes in a short time to adapt to various R angle requirements.
- Matching of cutter heads and R angles: We will prepare corresponding special cutter heads according to the radius and angle of the R angle required by the customer. These cutter heads are made of high-strength steel and are precisely polished to ensure that they can be evenly stressed when in contact with metal sheets, reducing the accuracy deviation caused by cutter head problems.
- Convenience of replacing cutter heads: Professionally trained technicians can usually control the time to replace a set of bending cutter heads within 30 minutes. For small batches and multiple specifications of orders, this fast switching capability greatly improves production efficiency and avoids long waiting times caused by mold replacement.
Key points of bending machine R angle processing: balancing efficiency and precision
Although bending machines are known for their flexibility, operating details are crucial to ensure flexibility while maximizing accuracy.
- Parameter setting: Accurately adjust the pressure, bending speed and stroke of the bending machine according to the material and thickness of the metal sheet. For example, when processing thicker carbon steel plates, it is necessary to increase the pressure and reduce the bending speed to avoid cracks in the plates; while processing thinner aluminum alloy plates, it is necessary to reduce the pressure to prevent excessive deformation of the plates. The setting of these parameters requires a combination of experience and calculation. We will quickly provide an adaptive parameter solution based on the database accumulated over the years.
- Cutter head installation calibration: After replacing the cutter head, strict calibration must be performed to ensure that the cutter head and the bending machine workbench are level and the error is controlled within a reasonable range. Inadequate calibration will cause uneven force on the plate, which will in turn affect the symmetry and accuracy of the R angle. We are equipped with special calibration tools, and we will perform detailed calibration after each replacement of the cutter head to minimize errors.
- Progressive bending techniques: For some special R angles, we will use a progressive bending method to gradually achieve the target shape through multiple small bends to avoid plate damage or precision deviation caused by one-time bending. Although this method will increase certain operating steps, it can effectively improve the bending quality, especially for small batch products with certain requirements for appearance and form.
Why choose a bending machine for R angle processing for small batch processing?
For customers who do not want to invest in molds for small-batch metal parts processing, bending machines are a very cost-effective choice for processing R angles.
- Significant cost advantages: It eliminates the design, manufacturing and maintenance costs of molds, only requires a small amount of tool head costs, and the tool heads can be reused, which can greatly reduce the unit cost of small-batch processing.
- Fast response speed: No need to wait for mold making, production can be arranged quickly after receiving an order, which can effectively shorten the delivery cycle for customers with urgent needs.
- Adapt to diverse needs: Whether it is R angles of different radii or composite R angles with special angles, bending machines can better meet them by replacing tool heads and adjusting operating parameters, especially suitable for small-batch processing needs in product research and development and trial production stages.
In the metal manufacturing industry, the demand for small-batch customization is increasing. Bending machines play an increasingly important role in the field of R angle processing with their flexibility and cost advantages. As a customized metal parts manufacturer with nearly 30 years of experience, Kailai Machinery has always focused on providing customers with more flexible and economical solutions by optimizing the bending process. If you need to process R angle of small batch metal parts and do not want to bear the mold cost, please contact us. We will use professional bending technology and rich metal manufacturing experience to provide you with satisfactory service.