We use cookies on our website to give you the most relevant experience by remembering your preferences and repeat visits. By clicking “Accept”, you consent to the use of ALL the cookies.
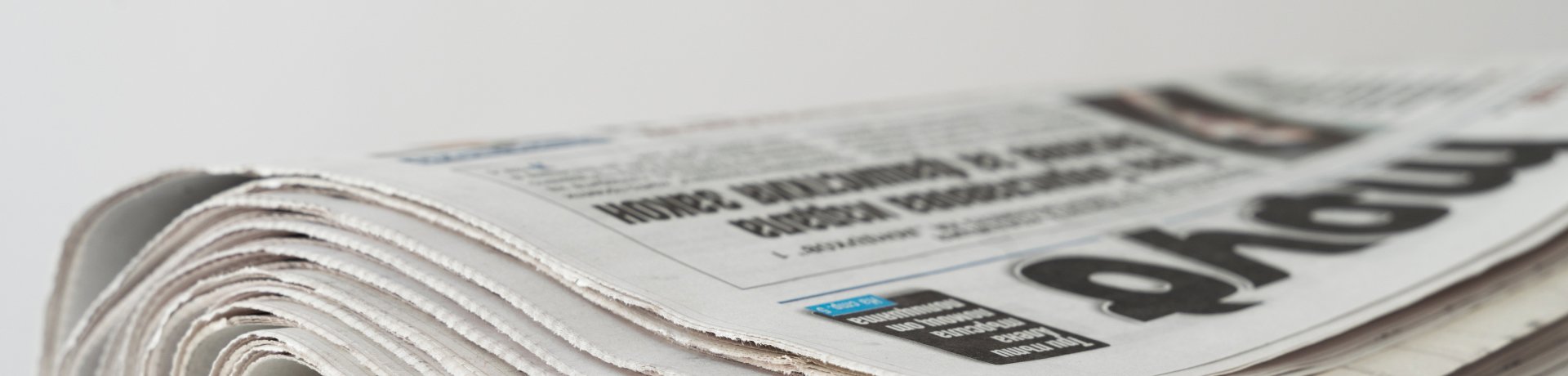
Laser cutting is an efficient, high-precision metal cutting process that is widely used in the sheet metal manufacturing industry. It uses a laser beam to thermally cut metal sheets, which has many advantages and some disadvantages. The advantages and disadvantages of the laser cutting process will be introduced in detail below.
advantage:
High precision: Laser cutting has extremely high cutting precision and can achieve precise cutting of metal sheets. The cutting edge is smooth and there are few burrs. It is suitable for product processing that requires high cutting precision.
Non-contact processing: Laser cutting is a non-contact processing method. The laser beam acts directly on the metal surface without causing mechanical deformation or damage to the workpiece, maintaining the integrity of the workpiece surface.
Wide applicability: Laser cutting is suitable for various metal materials, including steel, aluminum alloy, stainless steel, etc. It can also cut non-metal materials, such as plastic, wood, etc., and has strong versatility.
Fast cutting speed: Laser cutting speed is fast, it can efficiently complete a large number of cutting tasks, improve production efficiency, shorten the processing cycle, and is suitable for mass production.
High degree of automation: The laser cutting system can be integrated with automation equipment to realize automated production lines, improve production efficiency, reduce labor costs, and adapt to the development needs of modern manufacturing.
No need to cut molds: Unlike traditional cutting methods such as stamping and water cutting, laser cutting does not require cutting molds, which can save the time and cost of making molds and is suitable for small batch and multi-variety production.
Strong flexibility: Laser cutting can achieve cutting of complex shapes and can be freely cut according to product design requirements. It has high flexibility and strong adaptability.
shortcoming:
High equipment cost: The investment cost of laser cutting equipment is high, and the maintenance and operating costs are also high, which requires certain capital investment from the manufacturer.
Limited cutting thickness: Compared with other cutting methods, laser cutting has certain limitations on cutting thickness, and its cutting ability is limited for thicker metal sheets.
High environmental requirements: Laser cutting requires a relatively clean production environment and has high requirements for the work site, and certain safety protection measures need to be taken.
Large energy consumption: Laser cutting requires a large amount of energy, especially in high-power laser cutting, which consumes a lot of energy and puts certain pressure on the environment and energy resources.
High operating technical requirements: Laser cutting operators need to have a high technical level and operating experience, and be proficient in equipment operation and process parameter adjustment to ensure cutting quality and safety.
Heat-affected zone generated during the cutting process: Laser cutting will produce a heat-affected zone in the cutting area, which may cause metal degeneration, hardening and other problems, affecting the cutting quality.
In summary, the laser cutting process has the advantages of high precision, high efficiency, and wide applicability, but it also has the disadvantages of high equipment cost, limited cutting thickness, and high environmental requirements. When selecting a cutting process, it is necessary to comprehensively consider the product requirements and production conditions, and select the appropriate cutting method to achieve the best processing effect and economic benefits.